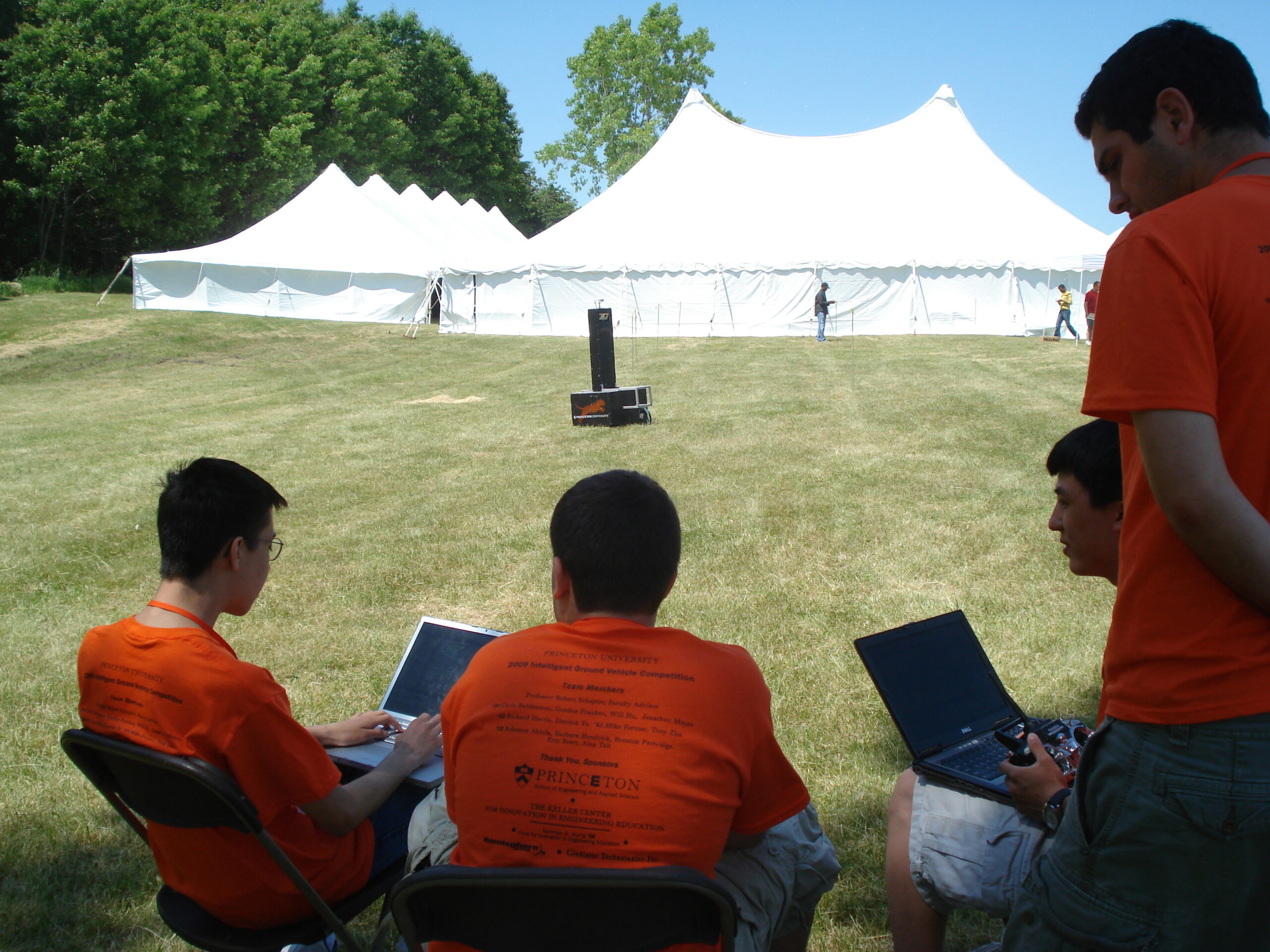
Argos
Following our successful rookie season with the IGVC, PAVE elected to compete in the 17th Annual IGVC, held in June, 2009. Our entry, named Argos, is an all-new robot based loosely upon the design of Kratos, our entry in the 2008 IGVC. This year’s team of student developers consisted of many newly recruited members. Starting in January, 2009, the team fabricated, built, and tested the robot in preparation for the competition.
As the second robot we designed for the IGVC, Argos had the benefit of borrowing from the successes of its predecessor, Kratos, as well as learning from its mistakes. constructing Argos from the ground up, which allowed us to avoid some of the design flaws from our previous entry.
Faculty Adviser: Professor Robert Schapire
Project Manager: Richard Harris
Logistics Coordinator: Alex Tait
Team Members: Chris Baldassano ’09 | Gordon Franken ’09 | Will Hu ’09 | Jonathan Mayer ’09 | Tom Yeung ’09 | Richard Harris ’10 | Derrick Yu ’10 | Michael Fortner ’11 | Solomon Abiola ’12 | Barbara Hendrick ’12 | Joshua Newman ’12 | Brenton Partridge ’12 | Eric Starr ’12 | Alex Tait ’12
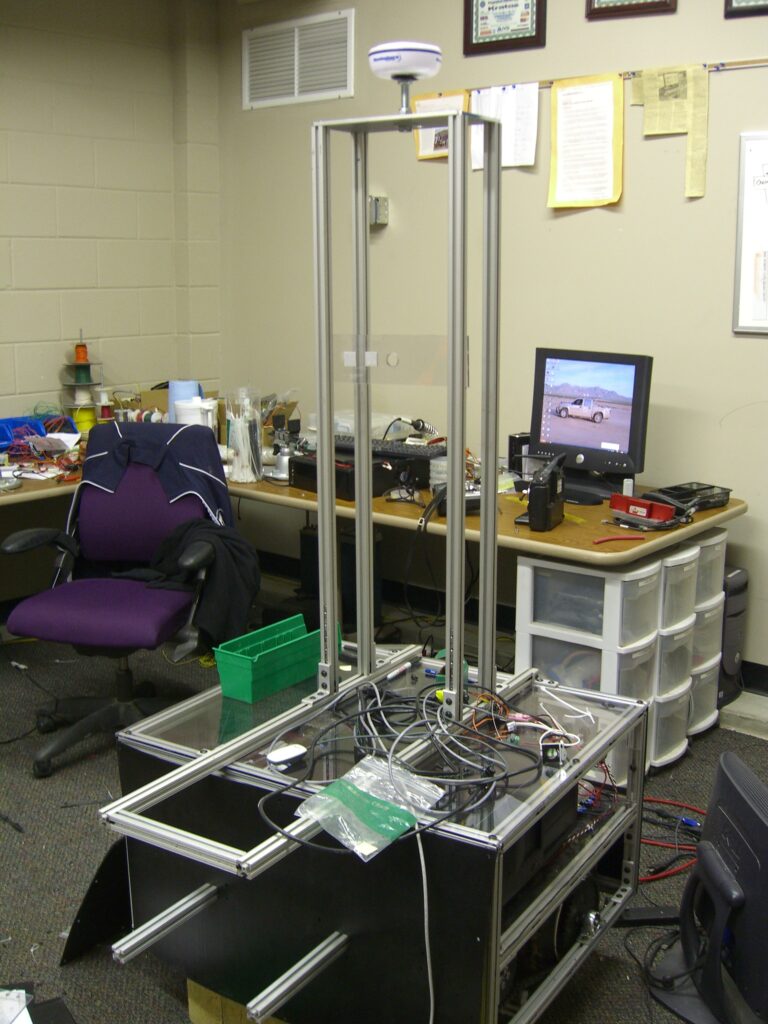
Chassis and Drivetrain
Unlike Kratos, the chassis of Argos was designed with exterior paneling in mind. The flat sides free from protruding aluminum brackets allowed the exterior panels to fit tightly to the frame. In addition, Argos is equipped with ventilation ports and exhaust fans to prevent overheating. Though much of the raw material for the frame was recycled from Kratos, the design WAS brand new. Argos was more compact and maneuverable than its predecessor; in fact, at 31 in wide, Argos fit through a standard doorway. A new bi-level layout allowed components to be located closer to the drive wheels, giving it a lower moment of inertia, while its taller sensor tower affords a better view of lanes and obstacles.
Argos boasted a new set of motors, powered by a 24-volt electrical system, that enabled it to accelerate faster than Kratos, and travel at the maximum allowed velocity for the competition. To prevent wheel slippage, its tires were upgraded to a knobbier tread, allowing for a better grip on the grass.
Sensors and Electronics
While Argos used the same state sensors (GPS, compass, and wheel encoders) as its predecessor, it also incorporated a Gladiator G50 MEMS gyroscope, which directly measured the instantaneous yaw rate, in order to correct for wheel slip. A LabJack data acquisition unit handled all digital I/O operations. Two Victor 885 motor controllers drove the robot’s motors. Argos also featured a redesigned emergency stop system, using a 2.4 GHz spread-spectrum wireless radio, which generated and encountered less interference than the 75 MHz analog radio used by Kratos. Relays plugged directly into the R/C radio channels and controlled the continuity of the signal between the LabJack and the motor controllers
Electronics and Computer Hardware
The new 24-volt electrical system was supplied by six 12-volt batteries in a series-parallel configuration and a 24-volt charger. The configuration allowed a maximum continuous runtime of 45 minutes at full power. Argos had a single computer, built with off-the-shelf components. An Intel quad-core processor paired with 6 GB of DDR3 RAM were sufficient to handle all of the computing tasks. Two 802.11g wireless routers provided Internet access to the onboard computer and allowed it to be accessed remotely.